Export Services
Premium Baled Bedding for High-Quality Compost Production
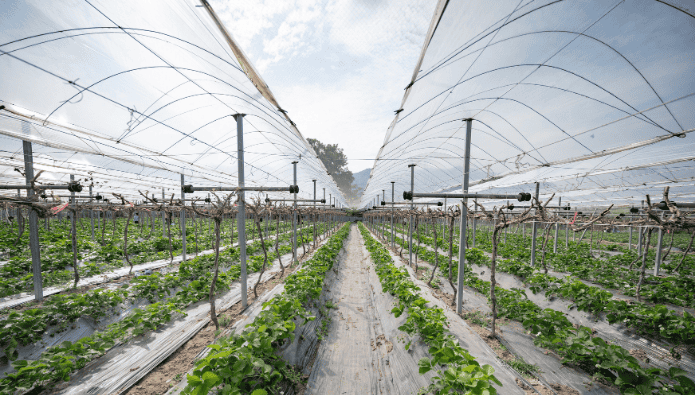
For over two decades, mushroom farms across the U.S. and Canada have relied on Charles T. Creech Services for baled used horse bedding—an essential ingredient in producing rich, productive compost. Our material, made from 99% damp straw and 1% horse manure, is baled to optimal size and weight for efficient transport and immediate use by commercial growers.
- Over 20 years serving mushroom farms
- Ideal compost blend: 99% straw, 1% manure
- Baled at 4’x4’x5’, approx. one ton each
- Up to 170 cubic yards per full trailer load
Get a free quotes
Our Process
Our baled horse bedding is prepared with precision and delivered with care. From collection to shipment, every step is designed to ensure mushroom farms receive consistent, high-quality composting material—on time and at scale.
01.
COLLECT & PREPARE BEDDING
We gather used horse bedding from trusted local stables and prepare it for processing at our Lexington facility.
02.
BALED FOR EFFICIENCY
The damp straw and manure mix is tightly baled into large, uniform blocks designed for maximum transport efficiency.
03.
SHIPPED TO GROWERS
Trailer loads are filled to optimal legal weight and delivered directly to mushroom farms across North America.